Abstract
A spatial state-space formulation based on the linear twodimensional piezoelasticity theory and involving local/global transfer matrices is applied to investigate the active vibration suppression of a simply supported, arbitrarily thick, orthotropic elastic beam, imperfectly integrated with spatially distributed piezoelectric actuator and sensor layers on its top and bottom surfaces, respectively. A linear spring-layer model is adopted to simulate the bonding imperfections between the host structure and the piezoelectric layers. To assist control system design, system identification is conducted by applying a frequency domain subspace approximation method with N4SID algorithm based on the first five structural modes of the system. The state space model is constructed from system identification and used for state estimation and development of control algorithm. A linear quadratic Gaussian (LQG) optimal controller is subsequently designed and simulated based on the identified model in order to actively control the response of the smart structure in both frequency and time domains.
vibration suppression; interfacial imperfection; exact solution; system identification; optimal control; Kalman observer
Active vibration control of an arbitrary thick piezolaminated beam with imperfectly integrated sensor and actuator layers
Seyyed M. HasheminejadI; M. VahediII; A. HoshangiIII
IAcoustics Research Laboratory, School of Mechanical Engineering Iran University of Science and Technology, Narmak, Tehran 16846-13114 Iran
IIDepartment of Mechanical Engineering, Saveh Branch, Islamic Azad University, Saveh, Iran vahedi.majid@gmail.com
IIIDepartment of Mechanical Engineering, Saveh Branch, Islamic Azad University, Saveh, Iran ahoshangi@yahoo.com
ABSTRACT
A spatial state-space formulation based on the linear twodimensional piezoelasticity theory and involving local/global transfer matrices is applied to investigate the active vibration suppression of a simply supported, arbitrarily thick, orthotropic elastic beam, imperfectly integrated with spatially distributed piezoelectric actuator and sensor layers on its top and bottom surfaces, respectively. A linear spring-layer model is adopted to simulate the bonding imperfections between the host structure and the piezoelectric layers. To assist control system design, system identification is conducted by applying a frequency domain subspace approximation method with N4SID algorithm based on the first five structural modes of the system. The state space model is constructed from system identification and used for state estimation and development of control algorithm. A linear quadratic Gaussian (LQG) optimal controller is subsequently designed and simulated based on the identified model in order to actively control the response of the smart structure in both frequency and time domains.
Keywords: vibration suppression, interfacial imperfection, exact solution, system identification, optimal control, Kalman observer.
1 INTRODUCTION
Measuring and control of distributed parameter systems (DPSs) using conventional spatially discrete sensors and actuators (e.g., accelerometers, strain gages, and pressure transducers, etc.) introduces various practical problems, especially if these devices are installed at (or near) modal nodes or lines of DPSs (Inman 1989). Some natural frequencies and mode shapes may be overlooked, and observability/controllability problems could occur. Consequently, development of spatially distributed sensors and actuators are highly crucial for structural identification and control of newgeneration high performance structures. Piezoelectric layers are excellent choices for distributed sensor and actuator applications, due to their great sensitivity and simple application to elastic continua. The distributed piezoelectric sensing element laminated on an elastic continuum reacts to mechanical strains and generates output voltage to actively monitor the structural oscillations on account of the direct piezoelectric effects. On the other hand, the distributed actuator element produces control forces/moments and restrains the undesirable structural vibrations through the converse piezoelectric phenomenon (Cady, (1946), Baileyand Hubbard (1985), Crawley (1987)). Recent literature reviews show that significant achievements have been obtained on distributed structural modelling, identification, and active vibration or shape control of smart beam, plate and shell structures integrated with spatially continuous piezoelectric sensor and actuator layers (Chee et al. (2000), Sunar and Rao (1999), Saravanos and Heyliger (1995), Kapuria and Yasin(2010), Bendary et al. (2010), Kerur and Ghosh(2011)). In the following paragraph, a brief overview regarding key contributions on active vibration control of smart composite beams, integrated (surface-bonded or embedded) with distributed piezoelectric sensor/actuator layers, is presented.
Peng et al. (1998) used a negative velocity feedback control algorithm in conjunction with a modal superposition technique and the Newmark method to formulate a finite element model based on third order laminate theory for the active position and vibration control of composite beams with distributed piezoelectric sensors and actuators. It was shown that in designing smart structures with distributed piezoelectric sensors/actuators, the positions and numbers of sensors/actuators have a vital effect on both shape and vibration control of the smart structures. For maximum effectiveness the sensor/actuator pairs must be located in high strain regions, far from regions of low strains. Bailey and Hubbard (1985) used a distributed-parameter control theory based on Lyapunov's second method to explore the feasibility of incorporating distributed piezoelectric actuators/sensors in smart structures. An experimental study on active vibration control of a cantilever beam with surface-bonded distributed piezoelectric polymer actuators was performed. A linear constant-gain controller was compared with a nonlinear constant-amplitude controller and it was found that under an equal voltage limit, the constant-amplitude controller increased the modal loss factor by more than an order of magnitude for small vibration levels, while it attained the same damping for large vibrations. Crawley and de Luis (1987) further explored the possibilities of using distributed piezoelectric actuators and sensors in smart structures, and carried out experimental and analytical studies on vibrational control of a classic clamped-clamped beam with embedded or surface bonded piezoelectrical sensors and actuators. In a series of papers, Tzou and coworkers (Tzou and Tseng (1991), Tzou and Tseng (1991), Tzou (1991), Tzou and Howard (1994)) derived and evaluated a generic layered shell theory for distributed sensing and vibration control of elastic multilayered continua (e.g., shells, plates, cylinders, beams, etc) integrated with distributed piezoelectric actuator and sensor layers based on Maxwell's principle, piezoelectricity theory, and Kirchhoff-Love theory. The authors developed a thin piezoelectric solid element with internal degrees of freedom for structural (modal) identification and vibration control of smart distributed parameter systems (e.g., beams, flexible robot manipulators, plates and shells), and verified their model by laboratory experiments for simple DPSs (i.e., cantilever beams and plates) coupled with thin distributed piezoelectric sensors/actuators. Two feedback control algorithms (namely, constant-gain and constant amplitude negative velocity feedback control) were generally integrated into their finite element formulations, and the efficiency of distributed piezoelectric sensors and actuators for distributed vibration control and identification of DPSs was demonstrated. Saravanos and Heyliger (1995) presented two distinct coupled discrete-layer formulations for finite element analysis of local and global electromechanical free vibration responses of composite beams with integrated piezoelectric sensors and actuators. Zhang and Sun (1996) developed an analytical model for sandwich beam structures containing shear piezoelectric actuator that resides in the entire core by modeling the facing sheets as classical Euler-Bernoulli beams and the central piezoelectric core as a Timoshenko beam. A closed form solution of the static deflection for a cantilever beam was presented and it was shown that the embedded shear actuators offer many advantages over surface mounted extension actuators. Aldraihem et al. (1997) utilized the finite element technique to study the distributed control of a cantilever laminated beam, and made comparisons between the Timoshenko and Euler-Bernoulli beam models. It was demonstrated that the higher order Timoshenko beam theory is superior in predicting the transient response of the beam, especially for beams of low aspect ratio. Also, use of an Euler-Bernoulli based controller to suppress beam vibration could cause instability through unintentional excitation of unmodelled modes. Smyser and Chandrashekharay (1997) utilized neural networks (NNs) to investigate robust vibration control of smart laminated composite beam with integrated piezoelectric sensors and actuators, using a higher-order shear deformation theory. The back-propagation algorithm was used to design and train offline an NN controller for imitating the performance of an LQG/LTR controller which was itself designed on the basis of a reduced-order state space model of the system obtained using the finite-element and mode superposition methods. Both NN and LQG/LTR controllers were shown to exhibit good performance robustness characteristics. Aldraihem and Khdeir (2000) proposed analytical models and exact solutions for beam bending problem, incorporating shear and extension piezoelectric actuators, based on two shear deformation theories, namely, the first-order and higher-order beam theories (FOBT, HOBT). Exact solutions were obtained by using the state space approach, and beam deflections for a variety of boundary conditions were examined. Shih (2000) used the modal expansion method to study the use of piezoelectric material as the distributed sensor and actuator for the active vibration control of a simply supported piezoelectric laminated curved beam using a one-dimensional curved beam theory. The effectiveness of active damping control and the sensor sensitivity were accessed with respect to various design parameters and it was demonstrated that the distributed surface bonded piezoelectric polymer layers can enhance the system damping and consequently effectively control the vibration levels. Balamurugan and Narayanan (2001) developed a finite element model based on Euler-Bernoulli beam theory to investigate the active vibration control of beam structures with distributed piezoelectric sensor and actuator layers integrated on the top and bottom surfaces of the beam. The control effectiveness and performance for three classical control strategies, namely direct proportional feedback, constant-gain negative velocity feedback, and an optimal (LQR) control strategy for various types of loading (i.e., impulse, step, harmonic, and random loadings) were studied. Sun and Huang (2001) presented an analytical model based on the Mindlin theory to study active vibration (negative velocity feedback) control of smart laminated composite beams with integrated piezoelectric (PVDF) sensor and actuator layers. Trindade et al. (2001) used a special finite element along with three different control algorithms, namely optimal (LQR, LQG) control with state feed-back, and derivative feedback control, for hybrid active-passive control of damped multilayer cantilever sandwich beams composed of a viscoelastic core sandwiched between layered piezoelectric skins. Wai sman and Abramovich (2002) considered the active stiffening effects in a general nonsymmetric piezolaminated composite beam consisting of piezoceramic layers bonded on the surface of the beam, using the first-order shear deformation theory (FSDT). It was demonstrated that the stiffness of the beam can be actively varied using the piezoelectric bonded actuators, causing major changes in the natural frequencies and mode shapes of the beam. It was also shown that the control of the first natural frequency of the beam is rather important, and when higher modes are considered, very large piezoelectric forces are required to produce a considerable change in the system natural frequencies. Sun and Mills (2002) utilized a torque actuator (involving proportional and derivative feedback control) along with a distributed piezoelectric polymer actuator (involving a linear velocity feedback control without mode truncation) for vibration suppression of a rotating cantilever flexible beam. Stability of the system was examined using a Lyapunov approach, and superiority of the linear velocity feedback control in comparison with the angular velocity feedback control for damping the dominant modes of vibration was demonstrated. Kang et al. (2002) used finite element method and optimal control theory to investigate the interaction between active and passive vibration control characteristics of laminated composite beams with collocated piezoceramic sensor and actuator layers. The damping and stiffness of the adhesive and the piezoceramic layers were simultaneously account for in the FEM formulation, and experimental verification was made through velocity feedback. It was concluded that the beam with higher bending stiffness can be more effectively controlled than the flexible beam when the feedback gain is large. Narayanan and Balamurugan (2003) presented finite element modeling for active vibration control of laminated beams with distributed piezoelectric sensor and actuator layers subjected to impact, harmonic and random excitations, using the first order shear deformation (Timoshenko) beam theory, and including thermoelectromechanical coupling effects. The effectiveness of the LQR optimal control scheme based on full state feedback in comparison with the less effective classical control methods like constant-gain negative velocity feedback was demonstrated. Hwu et al. (2004) derived analytical closedform solutions for the free and forced vibration of thick composite sandwich beams with surface bonded piezoelectric sensors and actuators, including the effects of transverse shear deformation and rotary inertia, and subsequently designed an observed-state feedback optimal control system (i.e., LQG/LTR controller with the Kalman filter) to suppress the vibration of composite beam. Chandiramani et al. (2010) adopted the higher-order shear deformation theory (HSDT) along with a modified Galerkin method to study the optimal (LQR) control of a composite rotating beam box (blade), comprised of an orthotropic (graphite-epoxy laminate) host structure with surface integrated and spanwise distributed piezoelectric (PZT-4) sensors and actuators, subject to a time dependent pressure pulse. It was found that structural tailoring can lead to a lower steady-state response at the cost of increased settling time. Chen et al. (2004) applied a new smart structure optimal (LQR) design strategy for robust vibration control of a pinned-pinned piezoelectric laminate beam by simultaneously optimizing the smart material distribution and the control system for extracting maximum performance from the closed-loop system. It was found that application of the segmented distributed (PVDF) sensors yields the best overall performance (i.e., decrease the spillover effect as well as increase the stability margin more efficiently). Lin and Nien (2005) used an instantaneous optimal close loop control algorithm to investigate modeling and vibration control of a laminated composite cantilever beam with integrated piezoelectric damping-modal actuators/sensors. A compensator based on the first three modes was employed to perform the shape control of the smart beam and attenuate the vibration spillover. Stavroulakis et al. (2005) developed a finite element model based on classical engineering beam bending theory and designed LQR and H2 optimal (robust) control strategies for active vibration control of a slender beam integrated with piezoelectric sensors and actuators on its upper and lower surfaces. The comparison between the two proposed control laws demonstrated that, while both strategies are successful, the second approach is favored due to its robustness characteristics. Edery-Azulay and Abramovich (2006) investigated the effects of continuous actuator and sensor piezo-layers performing in closed-loop, on the active damping of vibrating piezo-composite beams, using a first order shear deformation theory (FSDT). The accumulated voltage on the sensor layer was transferred to the piezoelectric actuator layer in order to actively attenuate the structural vibrations. The effect of extension and shear piezoelectric mechanisms, and also the feedback gain value on the active suppression of vibrating piezo-composite beam was investigated. Vasques and Rodrigues (2006) presented a finite element study on the active vibration control of smart three layer beams composed of isotropic materials with piezoelectric sensor and actuator layers, and made comparisons between classical and optimal linear quadratic Gaussian (LQG) feedback control strategies. Manjunath and Bandyopadhyay (2006) used Timoshenko beam theory, and finite element and state space methods to design a periodic output feedback (POF) controller for suppressing the first three modes of vibration of a flexible cantilever beam structure with embedded shear piezoelectric sensor and actuator layers. The effect of sensor location (while keeping the actuator location fixed) on the performance of the controller was evaluated and discussed. Zabihollah et al. (2007) used an experimental set-up along with a finite element model based on the coupled layerwise theories (LWTs) with layerwise linear variation of in-plane displacements to investigate optimal (LQR) vibration control of laminated piezoelectric composite beams. The LWTs was found to yield accurate results, while the computational cost amplifies with increasing the number of layers. Rao and Narayanan (2007) used the finite element model based on the transfer matrix approach to study the active flexural wave propagation control in multi-span uniform beams resting on periodically spaced, rigid simple supports with built-in distributed piezoelectric actuators and sensors, subjected to a moving harmonic pressure field. It was shown that by appropriate selection of the control gains, the response amplitudes at coincidence frequency can be actively controlled and also the widths and locations of the stop bands can be considerably inc reased. Zhang et al. (2008) presented results on LQG and robust H∞ control strategies for active vibration suppression of a flexible cantilever beam with surface-bonded piezoelectric sensors and actuators. The effectiveness and feasibility of the control methods were demonstrated through some simulation results. It was shown that robust H∞ control strategy has strong robustness with respect to modal parameter variations and also a good closed-loop dynamic performance in comparison with the LQG control method. Gharib et al. (2008) developed an analytical solution based on the firstorder shear deformation theory (FSDT) for analysis of functionally graded material (FGM) beams containing integrated layers of piezoelectric material acting as sensor and actuator. The dynamic response of the beam was examined and the effect of material constituent volume fraction on the deflection control of FGM beam was investigated. Marinova (2009) considered H2 and H∞ active vibration control of a flexible composite beam with built-in piezoelectric elements in the form of surface-bonded piezoelectric layers used as sensor and actuator, aiming for robustness with respect to parametric uncertainties and external loads. The discretization was carried out using finite elements, and the simulations were performed in the MATLAB environment demonstrating that the robust H2 and H∞ -controllers can achieve effective suppression of low-frequency disturbed vibrations of the composite beam while they preserve the efficiency in case of signal excessiveness due to high-frequency modes. Bendary et al. (2010) used the classical laminate (Euler-Bernoulli) beam theory to present a finite element model for the static and dynamic analysis of an intelligent advanced beam structure integrated with a distributed piezoelectric actuator layer and subjected to axial/transverse mechanical loads in addition to electrical load. The beam was composed of an isotropic and/or anisotropic substrate, completely or partially covered with the piezoelectric actuator layer. Kapuria and Yasin (2010), presented an efficient finite element model based on a layerwise theory with a quadratic variation of electric potential across the piezoelectric layers for active vibration control response of smart laminated cantilever beams integrated with electroded piezoelectric sensors and actuators. A reduced-order state space model is constructed and two control strategies, namely a constant gain velocity feedback (CGVF), and optimal LQR/LQG control strategy were considered for single-input-single-output (SISO) and multi-input-multi-output (MIMO) control configurations under step and impulse excitations. It was shown that multi-segment electrodes display faster attenuation in the closed-loop response than single-segment ones for all control laws. Also, the peak control voltages required for the same settling time are smaller in LQG control than the LQR control for both single and multi-segment electrodes. Zhang et al. (2010) proposed an effective procedure, based on the Linear Quadratic Gauss (LQG) optimal control approach, application of ANSYS software, and modal analysis, to suppress the vibrations of flexible intelligent cantilever beams with the piezoelectric sensors/actuators asymmetrically collocated on both sides of the same position of the host structure. Chandiramani (2004) investigated optimal LQR control of a thin-walled pre-twisted, doubly tapered, rotating beam comprised of an orthotropic host with surface-bonded transversely isotropic piezoelectric sensor-actuator pairs using a higher-order shear deformation theory (HSDT). Parametric studies on effects of ply-angle, rotation speed, pretwist, taper, rotor mass, and actuator saturation voltage limit, were performed. It was demonstrated that the HSDT, as compared to un-shearable and first-order shear models, provides conservative data on the lowest coupled natural frequencies, which is useful for passive and active control designs.
The above review suggests that (to the author's knowledge) nearly all investigators have so far employed the classical thin or various thick (shear deformation) beam theories in active vibration control of composite beams with integrated piezoelectric sensor/actuator layers. In this paper, a spatial state-space formulation based on the full (2D) exact elasticity (piezoelasticity) theory in conjunction with a frequency domain subspace identification scheme and linear optimal (LQG) control theory are applied for vibration control of a simply supported, arbitrary thick orthotropic elastic beam imperfectly bonded with (arbitrary thick) distributed piezoelectric actuator and sensor surface layers, and subjected to arbitrary electromechanical excitation. The proposed model is of noble interest as a canonical problem in structural vibration control, as it takes full account of the mechanical interaction between the sensor/actuator layers and the host structure. It is of particular value for vibration control engineers involved in development of reliable analytical and/or experimental tools for the design and analysis of thick piezo-laminated beams or panels with optimal vibrational control characteristics. Such components are of practical interest in development of smart microelectromechanical systems (MEMS) (Wang (1998), Zhang et al. (2006)), where a very accurate displacement control is required.
2 FORMULATION
An orthotropic beam (length L, total thickness H), bonded with piezoelectric actuator and sensor layers on its top and bottom surfaces and in state of plane stress, is considered (see Figure 1). The (Oxyz) coordinate system is set at the corner of the smart structure on the bottom surface of the sensor layer, as shown in Figure 1. Here, the nonzero stress components are σxx, σzz, and σxz only, which are independent of y. Also, there are additionally two nonzero y-independent electric displacement components Dx and Dz in the piezoelectric layers. In the following two subsections, the basic governing equations for the orthotropic host beam and the piezoelectric layers will be derived in (spatial) state-space form.
2.1 The spatial state space model
The linear piezoelectric coupling between the elastic field and the electric field can be expressed by the direct and the converse piezoelectric equations. In the state of plane-stress, the constitutive relations for the piezoelectric layers can be written as (Lim et al. (2005)):
where the pertinent piezoelectric constants, Cij, Qij , Gij, and the strain, ∈ij, and the electric field components, Ei, are respectively defined as
where φ is the electric potential, and U and W denote the axial and transverse displacement components, respectively (see Figure 1). Also, in the absence of body forces and free charge density, the equations of motion and the Gaussian equation of electric equilibrium are written as (Cheng et al. (2000))
where ψ = (U, W) is the displacement vector, ρ is the mass density, and Σ = [Σxx Σzz Σxz]T and De = [Dx Dz]T are the stress and electric displacement vectors, respectively.
Following the spatial state-space approach developed by Bahar (1975), by direct substitution of the kinematic relations (2b) into the constitutive relations (1), and subsequent incorporation of the results into the equations of motion/equilibrium (3), after some tedious manipulations, one advantageously arrives at
where V = [Σzz U Dz W Σxz φ]T, and
in which
Also, assuming simply supported end conditions, i.e.,
the state vector, V, may be expanded in the form(Bian et al. (2006))
where i = √-1, and ω is the radial frequency, and one should note that the piezoelectric constants Cs55 and Gs33 for the sensor material (see Eqs. 2a) are used as the normalization constants in the above equation and throughout the formulation. Substituting the above expansions into the state equation (4), yields
where ζ= z/H, and the vector (ζ) = [
zz

The solution to Eq. (7) is written as [48]
where ζs= hs/H and ζa =(hs + hh)/H (see Figure 1). Thus, using the above relations, the state variables at the lower surface of the sensor/actuator layer may simply be related to those at the upper surface in the form:
where Ms = exp (ζsAs) and Ma= exp [(1-ζa)Aa]
For the host orthotropic layer, one can readily follow the above procedure to drive the pertinent matrix equations. In the state of plane-stress, the constitutive relations for the orthotropic layer is provided in the Appendix. In particular, with the simply supported end condition assumption, the state vector, w, may be expanded in the form
and u and w denote the axial and transverse displacement components of the host layer, respectively (see Figure 1). Also, the modal state space Eq. (7) may be re-written for the orthotropic layer in the form = Ah
, in which
(ζ) = [
zzū
Thus, using the above relations, the state variables at the lower surface of the host layer may simply be related to those at the upper surface as:
where Mh = exp(ζaAh).
2.2 The interface/boundary conditions and the displacement response
In this paper, the bonding adhesives joining the distributed piezoelectric sensor/actuator layers to the host orthotropic layer are to be modeled as linear spring layers characterized by appropriate interface imperfection parameters (Ksx, KszKªx Kªx) (Librescu and Schmidt (2001)). Accordingly, the mechanical conditions at the two interfaces between the host structure and the piezoelectric actuator and sensor layers are respectively written as
where the indices "s" and "a" refer to the sensor and actuator layers, respectively. Also, by virtue of Eqs. (6) and (10), the interface conditions (13) can be written in the following matrix form
where
m = [


Next, we suppose that the laminated beam is subjected to a distributed dynamic normal mechanical harmonic load, q(x, t) = Q(x) exp(iωt), acting over the area (Lq< x < Lq + aq) on its top surface (actuator layer), while it is traction-free at the bottom surface (sensor layer) (see Figure 1). Thus, the load amplitude, Q(x), may be expanded as
where q= Q(x)sin (mπx/L) Also, the electric boundary condition for the piezoelectric actuator segment, distributed over the area (La< x < La+ aa) (see Figure 1), may be written as (Ray et al. (1992))
where ω is the angular frequency of the imposed electric potential, and the amplitude of the imposed electric potential may be expanded in the form
where
a =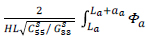
where the coefficient matrix Ta is given in the Appendix, Ra = (/Ma63) [Ma13Ma23Ma43Ma53]T, and Mija(ij=1,2,...6) denote the ij-th elements of the transfer matrix Ma. Furthermore, the electric boundary conditions for piezoelectric sensor are (Ray et al. (1992))
Moreover, by virtue of Eqs. (9a) and (19), after some manipulations, one obtains
where the coefficient matrix Ts is given in the Appendix. Finally, the state Eqs. (9), (12), (14), (18) and (20), may advantageously be combined to obtain the global transfer relation in the form
where S = TaPaMhPsTs is the 4×4 global transfer matrix pertaining to the laminated smart structure.
Now, by making use of the boundary conditions (15), (16), and (19) in the state Eq. (21), after some manipulations, one arrives at the following matrix relation for the displacement components at the lower surface of the sensor layer:
where Sm =, and Sij (i,j=1,2,...,4) refer to the elements of global transfer matrix S.
Thus, the displacement response of the system can readily be obtained from Eqs. (9) and (12). Direct implementation of Eqs. (22) into the state solution (9a), keeping in mind the mechanical and electrical boundary conditions for the sensor layer (i.e., Σszz=Σsxz = 0 at ζ= 0 and Dsz= 0 at ζ= 0 along with φs= 0 at ζ = ζ s), after some manipulations, one obtains the expression for the modal coefficient of the voltage at the lower surface of the sensor layer:
Thus, the average induced voltage in the sensor segment, which is distributed over the area (Ls< x < Ls + as) (see Figure 1), can be obtained by substituting Eq. (23) into Eq. (17) and integrating electric potential on sensor length in the form
where b is beam width and Cs(bε33/hs) as is the sensor capacitance.
2.3 System identification
In the last decades, subspace state-space identification methods, which can estimate the system order and matrices from input-output data without prior knowledge of the plant under study, have progressed significantly for identifying state-space models. The N4SID algorithm (Overschee and Moor (1994)) is one particular type of subspace algorithm whose numerical implementation is offered in Matlab's System Identification Toolbox (Ljung (2001)). It relies on subspace fitting strategies for the approximation of the extended observability matrix. In this paper, the above mentioned frequency domain subspace-based approximation scheme is applied to estimate system order and matrices of the entire fluid-structure coupled problem. The process begins with collection of openloop input-output (actuator/sensor voltage) data from experimental or numerical simulations. In particular, one can measure or calculate the sensor segment output voltage Vs (see Eq. 23), in response to an actuator segment input voltage signal φa, and use the data to identify the system state-space model. Accordingly, using the above procedure, the linear n-th order single input- single output (SISO) continuous time state space model of the piezo-laminated beam can be constructed in the form
where u(t) is the input vector (control signal), y(t) is the output vector (measured signal), x(t) ∈ Rn is the state vector, w(t) ∈ R is the exogenous input vector (e.g., reference signal, disturbances, noise, etc), and the system matrices A ∈ Rn×n, Bw ∈ Rn, Bu ∈ Rn×1, C ∈ R1×n, Dw ∈ R and Du ∈ R are estimated from the input vector u(t) and the output vector y(t), by utilizing Matlab's System Identification Toolbox, as explained above.
2.4 Controller design
In optimal control systems, the feedback control is directly designed to achieve the greatest possible reduction in the dynamic response of the smart structure. Frequently, however, the order of the state-space representation is unacceptably high and thus it is rarely used in structural dynamics.
Consequently, before designing the optimal controller, we shall consider the state-space representation based on the modal coordinates, where the number of equations is significantly lower, while the accuracy of the analysis has not suffered. Accordingly, following the standard procedure outlined by Gawronski (2004), the modal form of linear time-invariant (LTI) equations of motion (25), with the continuous system realization advantageously be written as
where is disturbance matrix, wn is the measurement noise, wd is associated with the disturbance signals (i.e., it may include actuator noise and/or any external random disturbance), and obtaining the modal state-space representation triple (Am, Bm , Cm) requires some relatively tedious manipulations, which is explained by Maciejowski (1989). Also, the measurement noise, wn, and the process noise, wd are generally assumed to be uncorrelated zero-mean Gaussian stochastic processes with constant power spectral density matrices, Wn and Wd , respectively. In other words, wn and wd are white noise processes with covariances
where E is the expectation operator and δ (t-τ) is the delta function.
The LQR problem, where all the states are known, is the deterministic initial value problem: Given the system z(t) = Am z(t)+ Bm u(t) with a given non-zero initial state z(0), find the input signal u(t) which puts the system back to the zero state (z = 0) in an optimal manner, i.e. by minimizing the deterministic cost
where Q and R are suitably chosen constant weighting matrices, such that Q = QT> 0, and R = RT> 0. The first step in the solution of the LQG problem consists of finding the optimal control to a deterministic linear quadratic regulator (LQR) problem: namely, the above LQG problem without wd and wn. The optimal solution to this problem can be written in terms of the simple state feedback law
where is the estimated state, and Kc= R-1BTmX , in which X (X = XT> 0) is the unique positive-semi definite solution of the algebraic Riccati equation
The next step is to find an optimal estimate of the state z, so that E{[z -
]T[z -
]} is minimized. The optimal state estimate is given by a Kalman filter, which estimates the state of the system in presence of noisy measurements, and is independent of Q and R. The Kalman filter has the structure of an ordinary state estimator or observer with:
where Ke= YCTmW-1n is the optimal choice for observer gain which minimizes the mean square error E {[z -]T [z -
]}, and Y = YT> 0 is the unique positive-semi definite solution of the estimator algebraic Riccati equation
Lastly, using the modal state-space realization (26), the state feedback law (29), and the estimated state equations (31), after some straight forward manipulations, one can obtain the closed-loop system dynamic equations in the form
where ε (t) = z(t) - (t). This shows that the closed-loop poles are simply the combination of the poles of the deterministic LQR system (eigenvalues of Am - Bm Kc) and the poles of the Kalman filter (eigenvalues of Am - KeCm), which is exactly as predicted by the Separation Theorem (Skogestad and (2005)). This completes the necessary background required for the analysis of the problem. Next, we consider some numerical examples.
3 RESULTS
In this section we consider some numerical examples. Realizing the large number of parameters involved here while keeping in view our computing hardware limitations, we confine our attention to a particular problem (see Figure 1). The host layer (hh = 0.003m, L = 0.6m)is assumed to be made of an orthotropic material with the material properties as given in Table 1 (Bian et al. (2006)). The actuator/sensor pair segments are assumed to be perfectly bonded(Ksx, Ksz, Kªx, Kªz= 0) on the upper/lower surfaces of the core orthotropic layer, with the following geometric ters:(ha = hs = 0.00025m, La = Ls = 0.48m, aa = as = 0.07m), and fabricated from Ba2NaNb5O15/ PZT4 with the mechanical and electrical material properties as given in Table 1.
Also, two types of external loads are considered: a uniformly distributed transverse impulse load, and a uniformly distributed transverse random (Gaussian) load. A general Mathematica code was constructed for computing the global modal transfer matrix, S = TaPaMhPsTs, obtaining the sensor modal displacement components (s,
s) from Eqs. (22), and ultimately calculating the average induced voltage in the sensor segment by numerical integration of Eq. (24). Computations were performed on a network of personal computer with a maximum truncation constant of mmax = 10 in Fourier expansions (6), (10), (15), (17) and (25) to assure convergence in the high frequency range. Before presenting the main results, the overall validity of the formulation should be demonstrated. To do this, we computed the sensor voltage amplitude, versus the excitation frequency for our three-layered Ba2NaNb5015-orthotropic-PZT4 beam subjected to either an external uniformly distributed constant amplitude transverse load (q(x, t) = 1eiωt N; Lq =0.2m, aq = 0.01m), or a uniformly distributed constant amplitude electrical load (φa(x, z = H, t) = 1eiωtV) applied on the actuator segment. The outcome, as shown in Figure 2 shows good agreements with those calculated by using the commercial finite element code ABAQUS (user's manual version 6.10). It is noteworthy that in the ABAQUS model, about 500 eight-node biquadratic plane stress 2D quadrilateral piezoelectric (CPS8RE) elements were used to model the sensor and actuator layers, and about 3000 eight-node biquadratic plane stress 2D quadrilateral (CPS8R) elements were used to modelorthotropic layer. In addition, mesh size sensitivity analysis was carried out for numerical convergence checking.
For the design and simulation of the control system, MATLAB® and Simulink softwares were utilized, and a Single-Input Single-Output (SISO) configuration, with the output being the voltage at the sensor segment location, and the input being the control voltage applied into the actuator segment of the top piezoelectric layer (see Figure 1), was considered. Next, we set the thicknesses of the top and bottom piezoelectric layers nearly equal to zero (ha = hs≈ 0) and computed the frequency response of a moderately thick simply supported 0º graphite-epoxy (AS4/3501-6) composite beam (hh = 0.0254m, L = 0.381m) subjected to an external uniformly distributed constant amplitude transverse load(q(x, t) = 100eiωt N; Lq = 0.06m, aq = 0.02m), with the material properties as given in Table 1 of Ref. Calim (2009). The first five calculated system resonance (peak) frequencies, as tabulated in the last column of Table 2a (the associated frequency response curve is not shown for briefness), demonstrate good agreements with those presented in Refs. (Calim (2009), Chandrashekhara and Bangera (1992), Rao and Ganesan (1997)) which are based on the high order shear deformation theories. As a further check, we set the thickness of the orthotropic core layer and the top piezoelectric actuator layer nearly equal to zero (ha = hs≈ 0) and computed the frequency response of a moderately thick simply supported unimorph BaTi03 piezoelectric beam (hs = 0.02m, L = 0.3m) subjected to an external uniformly distributed constant amplitude transverse load (q(x, t) = 100eiωt N; Lq= 0.06m, aq = 0.02m), with the material parameters as given in Table 1 of Ref. (Yang and Zhifei (2009)). The first four calculated system non-dimensional resonance frequencies,ωhs, as tabulated in the last column of Table 2b, demonstrate good agreements with those presented in Refs. (Yang and Zhifei (2009)) which were obtained using a state-space based differential quadrature method (SSDQM) and exact piezoelasticity theory.
For the design and simulation of the control system, Matlab software was utilized, and a Single-Input Single -Output (SISO) configuration, with the outputs being the voltages of the sensor segment, and the input being the control voltage applied into the actuator segment of the top piezoelectric layer (see Figure 1), was considered. Figure 3 compares the frequency response functions of real (elasticity solution) and identified (estimated) models. It is clear that the identified model, which considers only the first five structural modes, represents the dynamics of the system very well within the selected range (0 < f = ω/2π < 1000 Hz).
In the optimal control strategy, the relative magnitudes of Q and R are chosen to compromise the requirements on minimizing vibration energy against control voltage. The performance of the closed-loop system is classically defined through the closed-loop parameters such the bandwidth, the root-mean-square system response, or settling time and overshoot. These quantities are implicitly reflected in the weighting matrix, Q, in an obscure manner. Consequently, approximate relationships between weights and closed-loop performance may be derived for structures, giving guidelines as to how to determine the weights that shape the closed-loop system performance that meets the requirements. Figure 4 shows the frequency response magnitude (in dB) of closed-loop system for LQR weighting matrices (Q = QI, R = RI; Q = 108,109, 1010,R = 0.1,1) and for a fixed actuator/sensor interface imperfection parameter ( = 0). The most important observations are as follows. Decreasing the control input weighting factor R (i.e., relieving the bound restriction on the applied control force) leads to a notable decrease in the closed-loop frequency response amplitudes. Also increasing the weighting factor 108 < Q < 1010, has a prominent diminishing effect on the frequency response amplitudes. This reduction is observed to be most severe for the largest voltage amplitudes observed among the first five modes, which may be directly linked to the selected diagonal form of the state weighting matrix Q = QI. In other words, it is seen that the developed control mechanism has a significant influence on controlling all five modes, especially for Q= 1010, R = 0.1, where the response is completely eliminated. Lastly, it should be noted that the selected singlesegment sensor/actuator configuration is not suitable for simultaneous control of a wide range of vibration modes, and effective control in this situation requires more sensors/actuators or more complicated mathematical modeling of the smart system.
Finally, Figures 5a,b
display the vibration control performance of the simply-supported piezolaminate beam in the time domain for a white noise distributed mechanical disturbance with a PSD of 0.1 (N2-s/rad) and a sensor white noise with a PSD of 10-4 (N2-s/rad), by using LQG optimal control with selected weighting matrices (Q = QI, R = RI; Q = 108,109, 1010, R = 0.1,1) and for perfectly bonded actuator/sensor layers ( = 0). The corresponding voltages applied at the actuator location are also shown in the figure. Furthermore, in order to avoid the depolarization of the piezoelectric actuator, the maximum control voltage applied is set to 200Volts. The effectiveness of the LQG active control strategy for controlling the random vibration is clear. Comments very similar to the above remarks can readily be made. The most important distinction here is perhaps the observation of a maximum (minimum) variation in the actuator voltage level for Q= 1010,R = 0.1 (Q = 108, R = 1). In other words, a larger Q sets higher demand on control voltage, while a larger R further decreases the applied control effort.
4 CONCLUSIONS
Vibration control of an arbitrarily thick smart laminated beam structure with imperfectly bonded actuator/sensor surface layers and under harmonic electromechanical excitations has been performed using LQG optimal control strategy. A spatial state-space formulation based on the full elasticity (piezoelasticity) theory which incorporates appropriate local/global transfer matrices is developed to obtain the frequency response of the system. Subsequently, system identification is conducted by applying the MATLAB's N4SID subspace algorithm, followed by observer design and development of the optimal control algorithm. The control performance of the system is demonstrated in both frequency and time domains for an orthotropic beam asymmetrically collocated by a pair of piezoelectric actuator/sensor segments. It is demonstrate that the LQG control strategy with a single-segment actuator-sensor pair is very effective in suppressing the system time response and provides a notable overall improvement in the settling time, especially for higher values of state weighting factor Q . The selected diagonal form of the state weighting matrix (Q = QI) leads to effective suppression of the sensor voltage modes with the largest amplitudes, especially for the higher structural mode. Also, decreasing the control input weighting factor R leads to a notable decrease in the closed-loop frequency response amplitudes.
APPENDIX
where the indices "s" and "a" refer to the sensor and actuator layers, respectively, and the non-zero elements of coefficient matrices As,a are written as:
Clique para ampliar
Also, the constitutive stress-strain relations for the elastic orthotropic host layer, in the state of plane-stress, is written as
where C11= 11-
212/
22, C13 =
11-
12




where ph is the mass density of the host layer, and β = C11- C213/C33
Also,
where
Clique para ampliar
- ABAQUS, Analysis user's manual version 6.10 On-line Documentation.
- Aldraihem, O.J. Wetherhold, R.C. and Singh, T., (1997). Distributed control of laminated beams: timoshenko theory vs. euler-bernoulli theory. J. Intell Mater. Syst. Struct. 8:149-57.
- Aldraihem, O.J. and Khdeir, A.A., (2000). Smart beams with extension and thickness-shear piezoelectric actuators. Smart Mater. Struct. 9:1-9.
- Al-Saggaf, U.M. and Franklin, G.F., (1998). Model reduction via balanced realizations: an extension and frequency weighting techniques. IEEE Trans. Auto. Control. 7:687-692.
- Bailey, T. and Hubbard, J.E. (1985). Distributed piezoelectric polymer active vibration control of cantilever beam. AIAA J. Guid. Control Dyn. 8:605-611.
- Bahar, L.Y.A., (1975). State space approach to elasticity. J Franklin I. 299:33-41.
- Balamurugan V., Narayanan S., (2001). Active vibration control of piezolaminated smart beams Def. Sci. J. 51:103-114.
- Bendary, I.M. Elshafei, M.A. and Riad, A.M. , (2010). Finite element model of smart beams with distributed piezoe-lectric actuators. J. Intell. Mater. Syst. Struct 21:747-758.
- Bian, Z.G. Lim, C.W. and Chen, W.Q., (2006). On functionally graded beams with integrated surface piezoelectric layers. Compos. Struct. 72:39-351.
- Cady, W.G., (1946). Piezoelectricity. McGraw-Hill Book Company Inc (New York).
- Calim, F.F., (2009). Free and forced vibrations of non-uniform composite beams Compos. Struct. 88:413-423.
- Chandiramani, N.K. Librescu , L.I. Saxena , V. and Kumar A., (2004). Optimal vibration control of a rotating composite beam with distributed piezoelectric sensing and actuation. Smart Mater. Struct. 13:433-442.
- Chandiramani, N.K., (2010). Active control of a piezo-composite rotating beam using coupled plant Dynamics. J. Sound Vib. 329:2716-37.
- Chandrashekhara, K. and Bangera, KM., (1992). Free vibration of composite beams using a refined shear flexible beam element. Comput. Struct . 43:719-27.
- Chee, C. Tong, L. and Steven, G., (2000). A buildup voltage, (BVD) algorithm for shape control of smart plate structures. Eng. Struct. 24:5-11.
- Chen, W. Buehler, M. Parker, G. and Bettig, B., (2004). Optimal sensor design and control of piezoelectric laminate beams. IEEE Trans. Control Syst. Technol. 12:148-155.
- Cheng, Z.Q. Lim, C.W. and Kitipornchai, S., (2000). Three-dimensional asymptotic approach to inhomogeneous and laminated piezoelectric plates. Int. J. Solids Struct. 37:3153-75.
- Crawley, E.F. and Luis, J.D., (1987). Use of piezoelectric actuators as elements of intelligent structures. AIAA J. 25:1373-85.
- Edery-Azulay, L. and Abramovich, H., (2006). Active damping of piezo-composite beams. Compos. Struct. 74:458-466.
- Gawronski, W.K., (2004). Advanced structural dynamics and active control of structures, Springer-Verlag, New York, Inc.
- Gharib, A., Salehi, M. and Fazeli, S., (2008). Deflection control of functionally graded material beams with bonded piezoelectric sensors and actuators. Mater. Sci. Eng. A 498:110-114.
- Hwu, C. Chang, W.C. and Gai, H.S., (2004). Vibration suppression of composite sandwich beams. J. Sound Vib. 272:1-20.
- Inman, D. (1989). Vibration with control, measurement and stability. Prentice Hall, Englewood Cliffs, NJ.
- Kang, Y.K. Park, H.C. Kim, J. and Choi, S.B., (2002). Interaction of active and passive vibration control of laminat-ed composite beams with piezoceramics sensors/actuators. Mater. Des. 23:277-286.
- Kapuria, S. and Yasin, M.Y., (2010). Active vibration control of piezoelectric laminated beams with electroded actuators and sensors using an efficient finite element involving an electric node. Smart Mater. Struct. 19, art no. 045019.
- Kerur, S.B. and Ghosh, A. , (2011). Active control of geometrically non-linear transient response of smart laminated composite plate integrated with AFC actuator and PVDFsensor, J. Intel. Mater. Syst. Struc. 22:1149-1160.
- Lim, C.W.and Lau, C.W.H., (2005). A new two-dimensional model for electro-mechanical response of thick laminated piezoelectric actuator. Int. J. Solids Struct. 42:5589-5611.
- Librescu, L. and Schmidt, R., (2001). A general linear theory of laminated composite shells featuring interlaminar bonding imperfections. Int. J. Solids Struct. 38:3355-75.
- Lin, J.C. and Nien, M.H., (2005). Adaptive control of a composite cantilever beam with piezoelectric damping-modal actuators/sensors. Compos. Struct. 70:170-176.
- Ljung, L., (2001). System Identification Toolbox: for use with Matlab. Natick, MA: The MathWorks, Inc.
- Maciejowski, J.M., (1989). Multivariable feedback design, Addison Wesley, Great Britain.
- McKelvey, T. Akcay, H. and Ljung, L., (1996). Subspace-based multivariable system identification from frequency response data. IEEE Trans. Autom. Control. 41:960-979.
- Manjunath, T.C. and Bandyopadhyay, B., (2006). Vibration suppression of timoshenko beams with embedded piezo-electrics using POF. World Academy of Science, Engineering and Technology, 15:292-301.
- Marinova, D., (2009). Robust control of composite beams. Automat Rem Contr. 70:982-996.
- Narayan, S. and Balamurugan, V., (2003). Finite element modeling of piezolaminated smart structures for active vibration control with distributed sensors and actuators J. Sound Vib. 262:529-62.
- Overschee, P.V. and Moor, B.D., (1996). Continuous-time frequency domain subspace system identification," Signal Process. 52:179-194.
- Overschee P.V. and Moor B.D., (1994). N4SID: subspace algorithms for the identification of combined deterministic-stochastic systems. Automatica 30:75-93.
- Peng, X.Q. Lam, K.Y. and Liu, G.R., (1998). Active vibration control of composite beams with piezoelectrics: a finite element model with third order theory. J. Sound Vib. 209:635-650.
- Rao, M.S. and Narayanan, S., (2007). Active control of wave propagation in multi-span beams using distributed piezoelectric actuators and sensors. Smart Mater. Struc. 16:2577-94.
- Rao, SR. and Ganesan, N., (1997). Dynamic response of non-uniform composite beams. J. Sound Vib. 200:563-77.
- Ray, M.C. Rao, K.M. and Samanta, B., (1992). Exact analysis of coupled electroelastic behaviour of a piezoelectric plate under cylindrical bending. Compos. Struct. 45:667-677.
- Saravanos, D.A. and Heyliger, P.R., (1995). Coupled layerwise analysis of composite beams with embedded piezoelectric sensors and actuators. J. Intell. Mater. Syst. Struct. 6:350-363.
- Shih, H.R., (2000). Distributed vibration sensing and control of a piezoelectric laminated curved beam. Smart Mater. Struct. 9:761-6.
- Smyser, C. P. and Chandrashekharay, K., (1997). Robust vibration control of composite beams using piezoelectric devices and neural networks. Smart Mater. Struct. 6:178-189.
- Skogestad, S. and Postlethwaite I., (2005). Multivariable feedback control analysis and design. John-Wiley and Sons, (New York).
- Stavroulakis, G.E. Foutsitzic, G. Hadjigeorgiouc, E. Marinovad, D. and Baniotopoulose C.C., (2005). Design and robust optimal control of smart beams with application on vibrations suppression. Adv. Eng. Softw. 36:806-813.
- Sun, B. and Huang, D., (2001). Vibration suppression of laminated composite beams with a piezo-electric damping layer. Compos. Struct. 53:437-447.
- Sun, D. and Mills, J.K., (2002). Control of a rotating cantilever beam using a torque actuator and a distributed piezoelectric polymer actuator. App. Acoustics 63:885-899.
- Sunar, M. and Rao, S.S., (1999). Recent advances in sensing and control of flexible structures via piezoelectric materials technology. ASME Appl. Mech. Rev. 52:1-16.
- Trindade, M.A. Benjeddou, A. and Ohayon, R., (2001). Piezoelectric active vibration control of damped sandwich beams. J. Sound Vib. 246:653-77.
- Tzou, H.S. and Tseng, C.I., (1991). Distributed piezoelectric sensor/actuator design for dynamic measurement/control of distributed parameter systems: a finite element approach. J. Sound Vib. 138:17-34.
- Tzou, H.S. and Tseng, C.I., (1991). Distributed vibration control and identification of coupled elastic/piezoelectfuc systems: finite element formulation and applications. Mech. Sys. Signal Pr. 5:215-231.
- Tzou, H.S., (1991). Distributed vibration control and identification of coupled elastic/piezoelectric shells: theory and experiment. Mech. Sys. Signal Pr. 5:199-214.
- Tzou, H.S. and Howard, R.V., (1994). A piezothermoelastic thin shell theory applied to active structures. ASME J. Vib. Acoust. 116:295-302.
- Vasques, C.M.A. and Rodrigues, J.D., (2006). Active vibration control of smart piezoelectric beams: comparison of classical and optimal feedback control strategies. Comput. Struct. 84:1402-14.
- Waisman, H. and Abramovich, H., (2002). Active stiffening of laminated composite beams using piezoelectric actuators. Compos. Struct. 58:109-120.
- Wang, P.K.C., (1998). Feedback control of vibrations in a micro machined cantilever beam with electrostatic actuators. J. Sound Vib. 213:537-550.
- Yang, L. and Zhifei, S., (2009). Free vibration of a functionally graded piezoelectric beam via state-space based differential quadrature. Compos. Struct. 87,257-264
- Zabihollah, A. Sedagahti, R. and Ganesan, R., (2007). Active vibration suppression of smart laminated beams using layerwise theory and an optimal control strategy. Smart Mater. Struct. 16:2190-2201.
- Zhang, Y., Xie, S. and Zhang X., (2008). Vibration control of a simply supported cylindrical shell using a laminated piezoelectric actuator. Acta Mech. 196:87-101.
- Zhang, J. He, H. and Wang, E., (2010). Active vibration control of piezoelectric intelligent structures. Comp. Struct. 5:401-409.
- Zhang, X.D. and Sun, C.T., (1996). Formulation of an Adaptive Sandwich Beam. Smart Mater. Struct. 5:814-823.
- Zhang, W. Meng, G. and Li, H., (2006). Adaptive vibration control of micro-cantilever beam with piezoelectric actuator in MEMS. Int. J. Adv. Manuf. Technol. 28:321-327.
Publication Dates
-
Publication in this collection
08 Dec 2014 -
Date of issue
2014